Stainless steel is a type of alloy where the primary material is iron, containing a minimum 11% of chromium which prevents rust and provides heat resistance properties to the material.
Alloys of stainless steel always contain different materials like carbon, nitrogen, aluminium silicon, sulfur, titanium, nickel, copper, selenium, and molybdenum.
On the basis of their properties, they are designated under various steel families which are primarily classified by their crystalline structure.
Types of stainless steels:-
- Austenitic stainless steel
- Ferritic stainless steel
- Martensitic stainless steel
- Duplex stainless steel
- Precipitation Hardening stainless steel (PH)
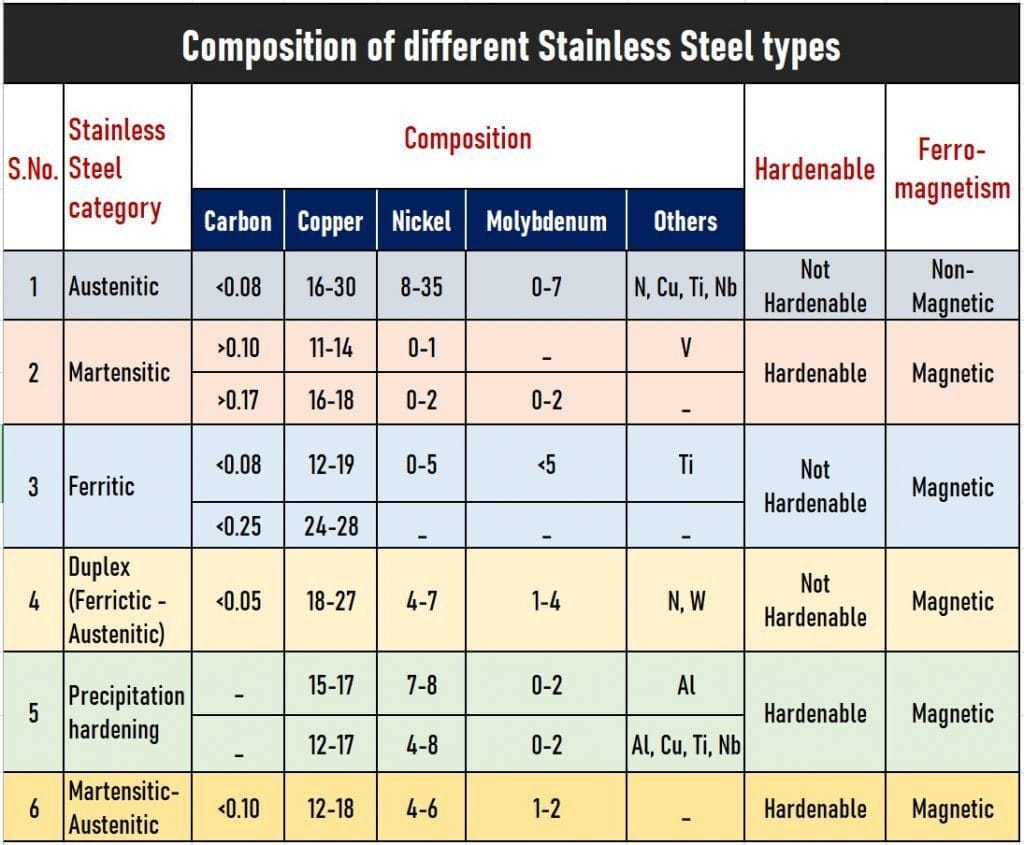
Before Understanding the difference between various steel grades we must first understand their properties, specifications, applications and their abilities, etc.
1- Austenitic stainless steel
In Austenitic type, stainless steel containing chromium and nickel are identified as 300 series whereas alloys containing chromium, nickel, and magnesium are identified as 200 series types
They contain 15% to 30% chromium and 2% to 20% nickel for enhanced surface quality, formability, and increased corrosion and wear resistance.
The stainless steels in the austenitic group have different compositions and properties but many common characteristics-
- They can be hardened by cold working but not by heat treatment
- In the annealed condition all are essentially not magnetic.
- They have excellent corrosion resistance with good formability and strength as a result of cold work
Note:
Type 304 and 316 are the most widely used alloy of the austenitic group.
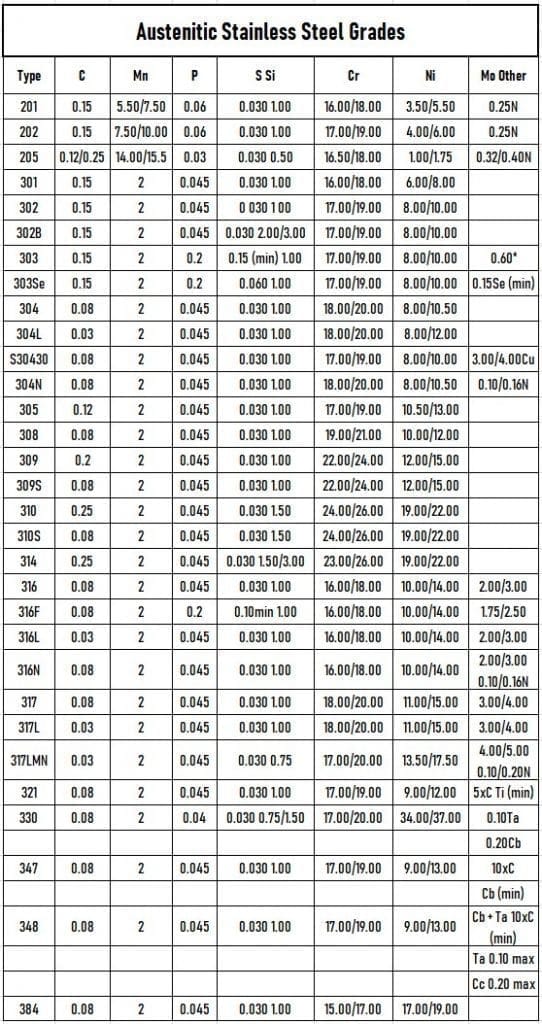
2- Ferritic stainless steel
Ferritic stainless steel is a straight chromium 400 series type that cannot be hardened by heat treatment and can only be moderately hardened by cold working.
Note:
They contain 15% to 30% chromium and 2% to 20% nickel for enhanced surface quality, formability, and increased corrosion and wear resistance.
This group of steels in the 400 series contains 10.5% to > 30% chromium for corrosion scaling at elevated temperatures and resistance.
They are magnetic and possess very good ductility and resistance towards corrosion and oxidation.
Note-
Type 430 is the most general ferritic stainless steel used.
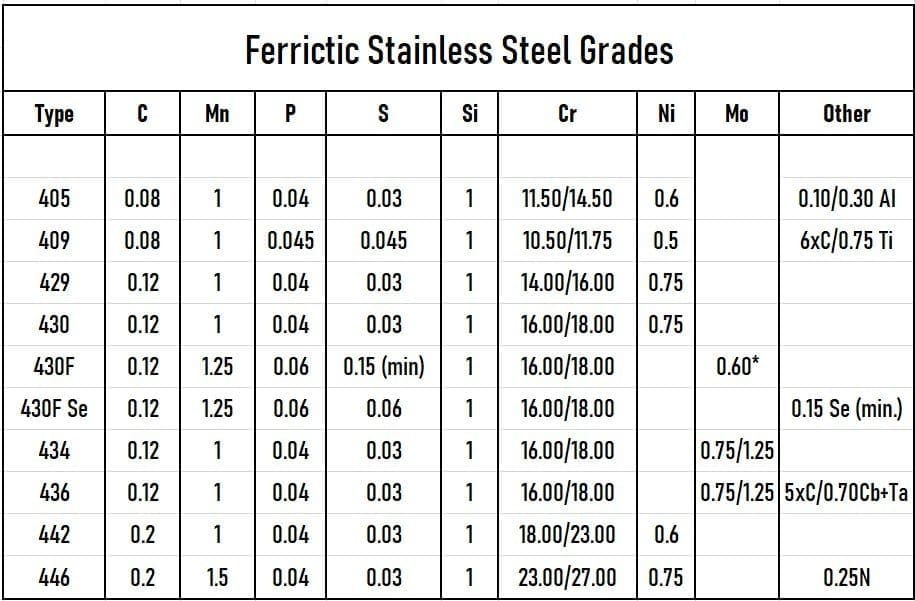
3- Martensitic stainless steel
Martensitic stainless steel are straight-chromium 400 series types.
They are hardened using heat treatment and are magnetic in nature.
They resist corrosion in mild environments, they usually contain a minimum of 11.5% up to 18% chromium and have higher levels of carbon than ferritic.
They have relatively good ductility, some alloys can be heat treated to tensile strengths exceeding 200,000 PSI.
Note:
Type 410 is the most general alloy used of the martensitic group.
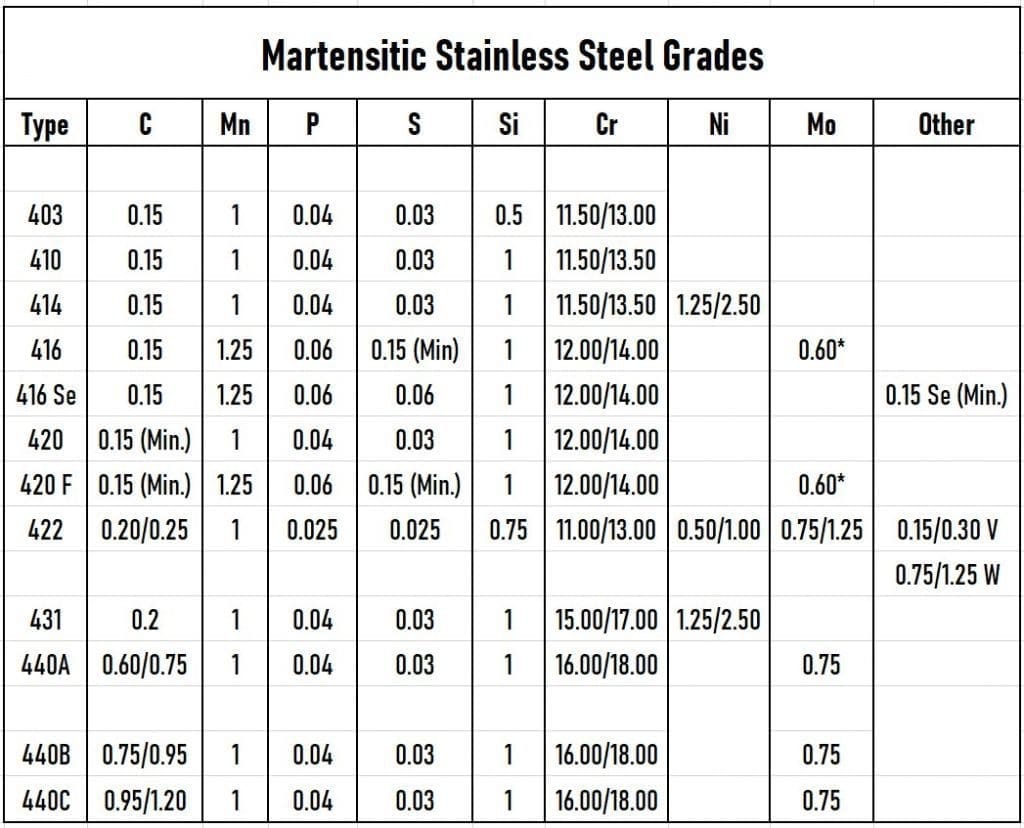
4- Duplex stainless steel
Duplex stainless steels have an annealed structure which comprises equal parts of austenite and ferrite
Duplex stainless steel offers several advantages over the common austenitic stainless steels which are-
- Highly resistant to chloride stress corrosion cracking
- Have excellent pitting and corrosion resistance and exhibit about twice the yield strength as conventional grades.
Note-
Type 329 and 2205 are the most general duplex stainless steel used.
5- Precipitation hardening stainless steel (PH)
There are two general areas of PH grade stainless steels: martensitic and semi-austenitic.
Precipitation hardened stainless steels are chromium-nickel types, some containing other alloying elements such as copper or aluminium.
They can be hardened by solution treating and ageing to high strength.
Stainless Steel Grade Chart
Steel Grades (3CR12, 201, 301, 302, 303, 304. 309, 316, 317, 321, 400, 409, 410, 420, 430, 431, 434, 436, 439, 440, 444, 904, 2205, 41003, UR52N)
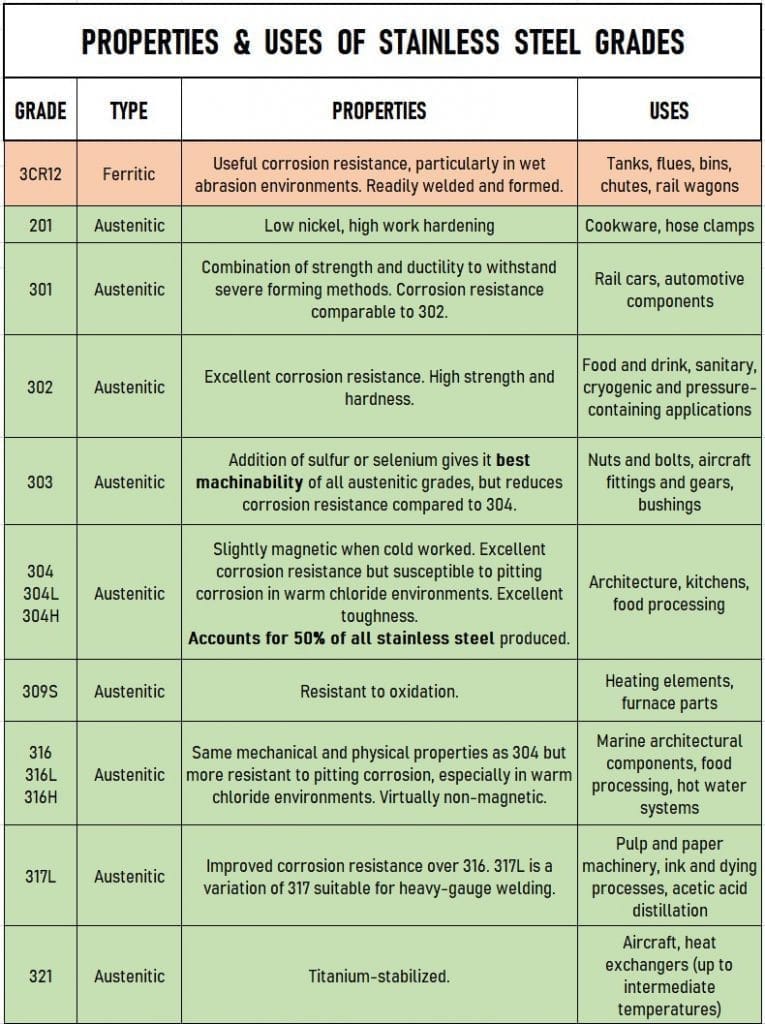
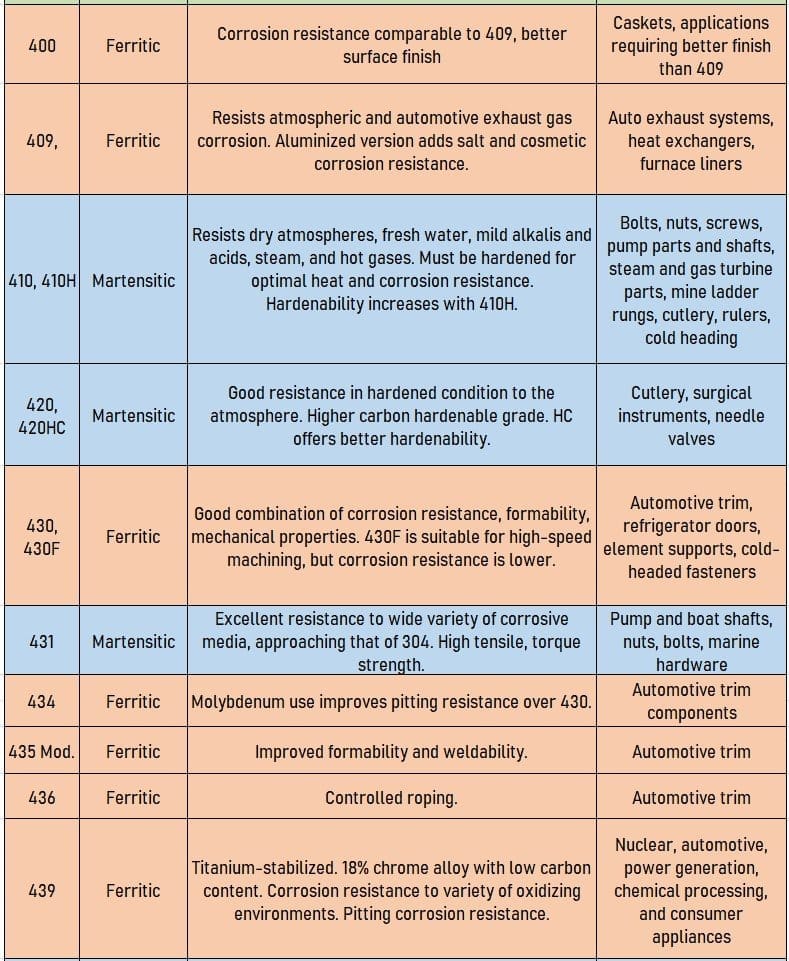
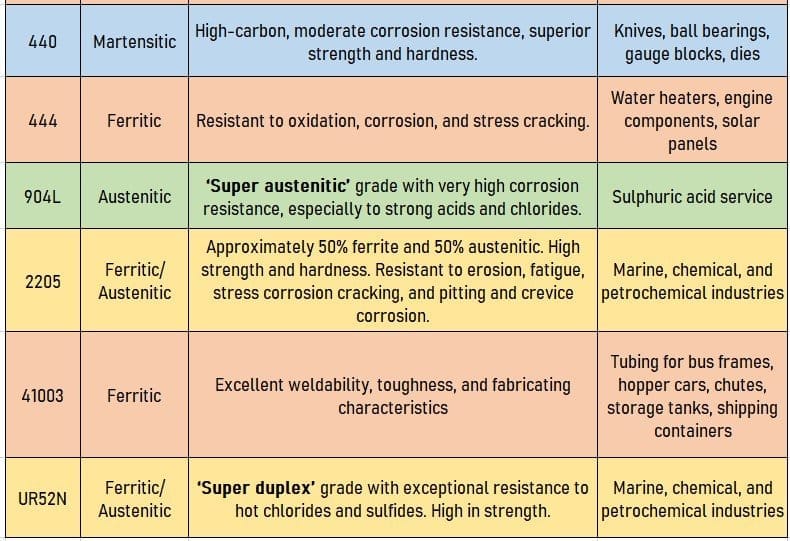
Stainless Steel Grade 304
Type 304 serves a wide range of applications. It withstands ordinary rusting in architecture, it is resistant to food-processing environments (except possibly for high-temperature conditions involving high acid and chloride contents).
It resists organic chemicals, dyestuffs, and a wide variety of inorganic chemicals.
Type 304 L (low carbon)
It resists nitric acid well and sulfuric acids at moderate temperature and concentrations.
It is used extensively for the storage of liquified gases, equipment for use at cryogenic temperatures (304N), appliances and other consumer products, kitchen equipment, hospital equipment, transportation, and waste-water treatment.
Note:
Type 304 is satisfactory for low temperatures, but Type 316 or Type 317 is needed for high temperatures.
Stainless Steel Grade 316
Type 316 contains slightly more nickel than Type 304, and 2-3% molybdenum giving it better resistance to corrosion than Type 304, especially in chloride environments that tend to cause pitting.
Type 316 was developed for use in sulfite pulp mills because it resists sulfuric acid compounds. Its use has been broadened, however, to handling many chemicals in the process .
Properties-
- Rutile coating
- Excellent all positional operability
- 140% high recovery version
- Primary intended for resistance to intergranular corrosion
Note:
Type 316 is usually used for reactors, fractionating columns, traps, baffles, caps, and piping.
Stainless Steel Grade 317
Type 317 contains 3-4% molybdenum (higher levels are also available in this series) and more chromium than Type 316 for even better resistance to pitting and crevice corrosion.
Properties-
- High pitting corrosion resistance as compared to 316
- Thin coated
- Excellent fully positional operability
Stainless Steel Grade 410
Type 410 has the lowest alloy content of the three general-purpose stainless steels and is selected for highly stressed parts needing the combination of strength and corrosion resistance, such as fasteners.
Type 410 resists corrosion in mild atmospheres, steam, and many mild chemical environments.
Stainless Steel Grade 430
Type 430 has lower alloy content than Type 304 and is used for highly polished trim applications in mild atmospheres.
Characteristics of different grades of Stainless Steels
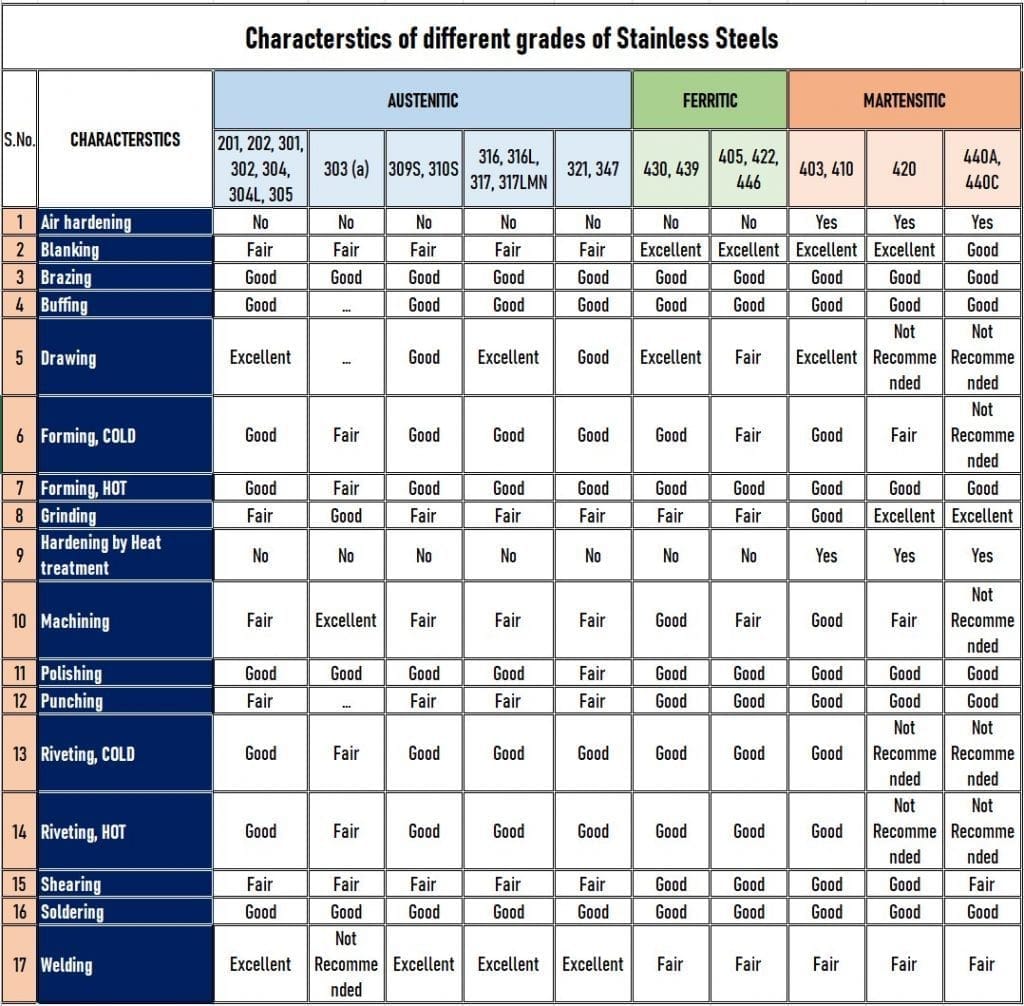
How to select the best Stainless steel for use
Selection of best stainless steel for use can be a difficult process, so to make it easy we can start by understanding the basic criteria which need to be kept in mind during the selection process.
The selection of stainless steel is done on the basis of corrosion resistance, fabrication characteristics, availability, mechanical properties in specific temperature, welding properties, cost, etc.
Note:
However, corrosion resistance and mechanical properties are usually the most important factors.
Characteristics to be considered in the selection of stainless steel for a specific application includes-
- Resistance to oxidation and sulfur reaction
- Corrosion resistance
- physical property characteristics such as thermal conductivity magnetic properties and electric resistivity
- Strength and ductility
- Toughness
- Resistance to abrasion erosion and galling
- Suitability of cleaning procedures
- It’s total cost including initial cost installation cost and the effective life expectancy of the finished product
- Its Availability in the market
- Fabrication characteristics.
Note:
Make sure to remember these points when you are purchasing any kind of stainless steel for your personal or for professional use.
Different alloying elements and their effect on stainless steel
Different alloying elements are used to form different types and grades of stainless steels used for different applications, as per the applications the alloying elements are added to the steel.
Effect of the alloying elements are listed below-
Chromium: Cr
Chromium forms a surface film of chromium oxide to make the stainless steel corrosion-resistant. It also increases the scaling resistance at elevated temperatures.
Nickel: Ni
Nickel stabilizes the austenitic structure and increases ductility, making stainless steel easier to form. It increases high-temperature strength and corrosion resistance, particularly in industrial and marine atmospheres, chemical, food, and textile processing industries.
Silicon: Si
Silicon increases scaling resistance by forming a tight initial scale, which will withstand cyclic temperature changes. It resists carburizing at high temperatures and slightly increases tensile strength and hardness. Small amounts of silicon are added to all grades of stainless for deoxidizing.
Manganese: Mn
Manganese promotes the stability of austenite, at or near room temperature and improves hot working properties. The addition of up to 2% manganese has no effect on strength, ductility, and toughness. Manganese is important as a partial replacement of nickel in 200 series stainless steel grades.
Molybdenum: Mo
Molybdenum increases corrosion resistance, strength at elevated temperatures, and creep resistance. It expands the range of passivity and counteracts the tendency to pit, especially in chloride environments.
Aluminium: Al
Aluminium is a very strong ferrite former and lowers the hardenability of stainless steel. It improves scaling resistance.
Carbon: C
Carbon strengthens stainless steel but promotes the formation of precipitates harmful to corrosion resistance.
Niobium: Nb
Niobium (Columbium) combines with carbon to reduce susceptibility to intergranular corrosion. It acts as a grain refiner and promotes the formation of ferrite.
Copper: Cu
Copper is added to stainless steel to increase its resistance to certain corrosive environments. It also decreases susceptibility to stress corrosion cracking and provides age-hardening effects. Can be used to control work hardening.
Titanium: Ti
Titanium combines with carbon to reduce susceptibility to intergranular corrosion. It acts as a grain refiner and promotes the formation of ferrite.