Weldability of Aluminum
The weldability, also known as joinability, it refers to the joining properties of the material to be welded and also selecting the best suitable welding method to weld that material.
TIG (Tungsten Inert gas Welding) is best suitable to weld aluminum and aluminum alloys.
It is difficult to determine the weldability of aluminum and aluminum alloys as weldability depends on the following factors-
- The shape of the parts to be welded
- The welding method
- The filler material
- The type of alloy
- the degree of freedom of movement of the parts during welding
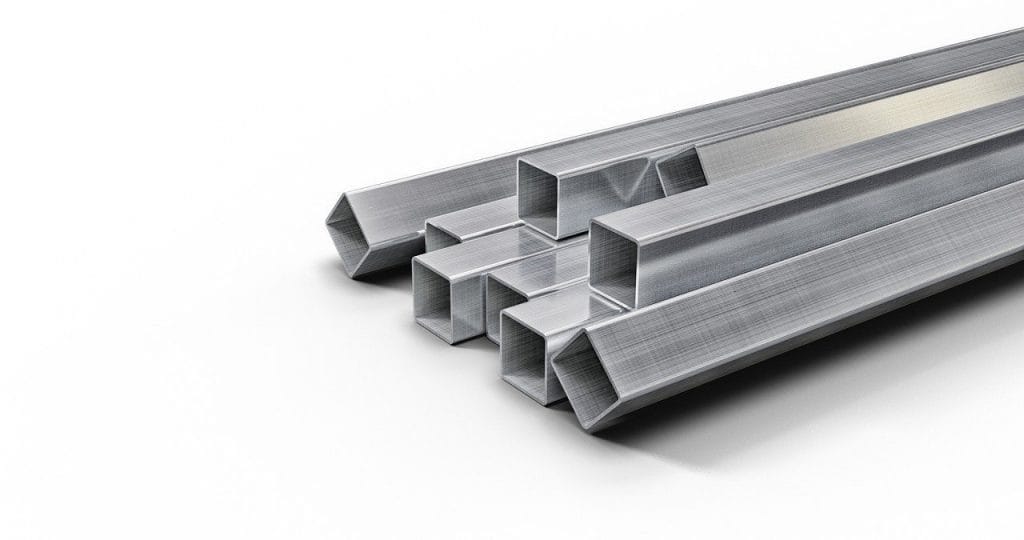
Types of welding used to weld Aluminum
There are generally 7 types of welding used to weld aluminum:
- TIG / GTAW welding
- MIG / GMAW welding
- Electron beam welding
- Laser beam welding
- Resistance (Spot & Seam) welding
- Soldering & Brazing
Among all MIG, TIG, and resistance (spot) welding is the most commonly used method in industry to weld aluminum.
Materials can be welded up to a maximum thickness of 50 mm using MIG and TIG welding.
1- Using TIG welding to weld Aluminium
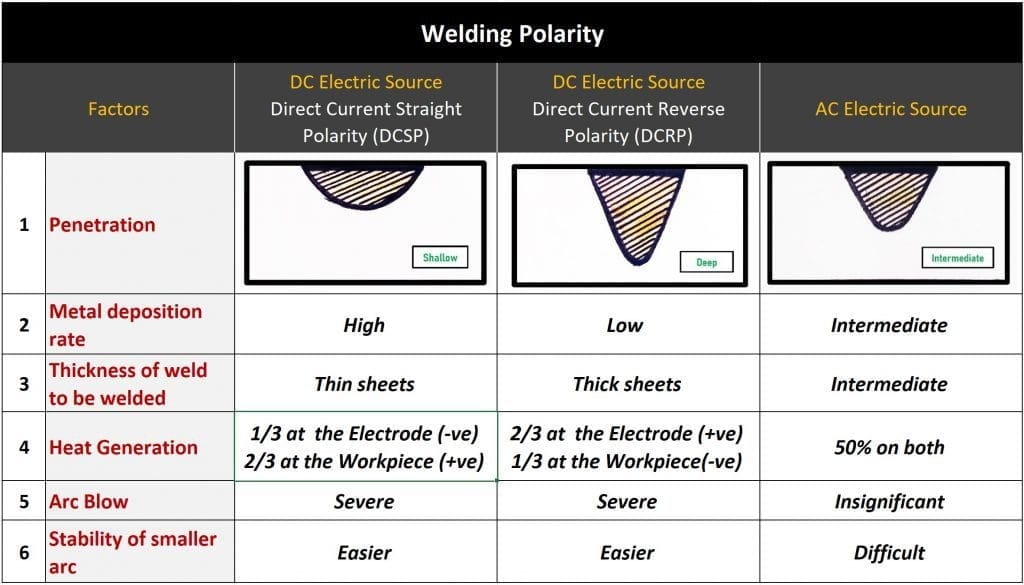
TIG is one of the best welding methods when it comes to weld aluminum.
To weld aluminium, TIG is used in two configurations:-
- DC power source as Direct current reverse polarity (DCRP)
- AC power source
By using the above two configurations the oxide formation is not severe, which means that electrons can easily be transferred from electrode to base plate this advantage will result in reducing welding defects such as pores, cracks, and inclusions.
The weld pool is protected by the atmosphere of inert gases such as helium, neon, argon, nitrogen, and carbon dioxide, etc.
Using TIG welding we can easily weld aluminum in all positions of a complex/non-complex part because the thickness of the weld bead is less.
During the welding, the movement of electrodes with respect to the workpiece will be controlled manually which means that we will have to use a constant-current type transformer where arc current will be controlled by the transformer.
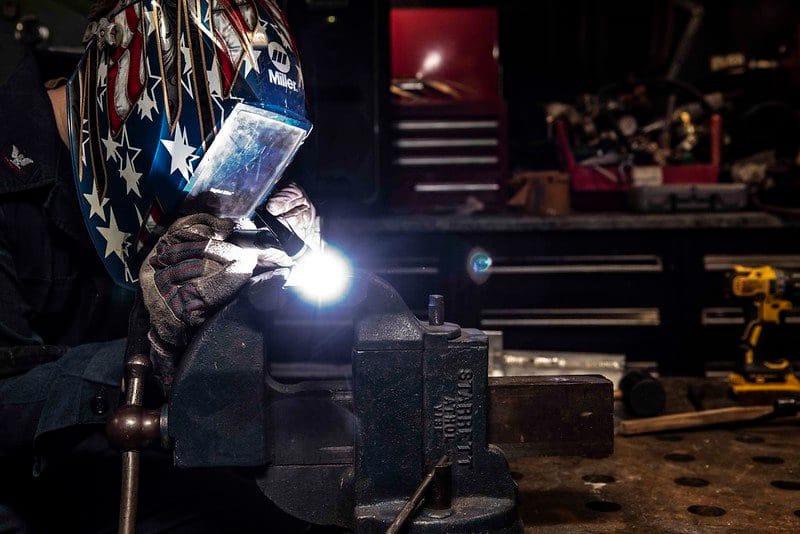
TIG ( Tungsten Inert Gas) Welding PRO Guide | Working & Application
2- Using MIG welding to weld Aluminum
In Metal inert gas welding (MIG) or Gas metal arc welding (GMAW) the aluminum is welded using a DC power source with Direct current reverse polarity (DCRP) configuration which means that there will be less heat concentration on the base material which result in less oxide formation, as excess oxide formation is not good for welding as it can result in welding cracks, poor resistance towards corrosion, porosity, and inclusions.
MIG is a form of automatic welding where the consumable bare aluminum wire is is fed automatically through a nozzle into the welding arc, the welding arc is shielded by an atmosphere of inert gases such as argon, helium, carbon dioxide, or a mixture of various other gases.
Have a look to above chart to have better understanding of welding polarities.
3- Using Electron welding to weld Aluminum
In an electron beam welding, a beam of electrons is used to melt the metal where it has to be welded, the electrons are generated with a help of a tungsten electrode and a cup-shaped cathode.
Application
Electron beam welding is used to weld aluminum for space industries, nuclear missiles, aircraft industries because of its high precision and accuracy.
Advantages
- Less heat affected zone
- High depth of cut
- Excellent precision and accuracy
Disadvantages
- It is an extremely costly setup because the electron beam welding is performed in an enclosed chamber where it is necessary to maintain a vacuum because the high energy electrons which are used to generate heat will collide with air particles due to which the electrons will lose all their energy.
- It emits X rays, that can harm our health if proper measures are not being taken.
4- Using Laser beam welding to weld Aluminum
In laser beam welding to weld aluminum and other metals, a coherent light beam is used to melt the desired spot where metal needs to be welded.
Application
- It is used welding copper and aluminum alloys in electric industries aircraft industries
- Making of precision tools.
- Used to weld other metals like high carbon steel, titanium, stainless steel, etc.
Advantages
- The major advantage of using electron and laser beam welding is that a deeper penetration can be obtained with very insignificant heat-affected zones.
- Excellent precision and accuracy are achieved with good quality of welds.
- Welds produced with laser welding have very good strength and are free of porosity.
- High Welding speed
- Laser beams can easily be shaped, manipulated, and focused optically, so the process can be automated.
Note:
The welding speed can range from 2.5m/min to as high as 80m/min for thin metals.
Disadvantage
- This is a less costly process than electron beam welding but still costly as compared to other aluminum welding methods.
Note:
Make sure to use electron welding or laser beam welding only if you require an excellent level of precision and accuracy with a high depth of penetration along with the finest welding results.
5- Using Resistance welding to weld Aluminum
- In resistance welding, the heat required for welding is produced by the means of electrical resistance across the two components which need to be joined.
- The major advantage of using resistance welding is that they do not require any filler material flux for shielding gas.
- Resistance welding is most commonly used to weld aluminum and steel in automobile industries by process of spot welding and seam welding.
Note:
Aluminum and copper have very high thermal conductivity so they require very high heat concentration, the current used in resistance welding operations for welding aluminum and magnesium can be as high as 10000 amperes.
6- Using Soldering and Brazing to weld Aluminum
Soldering
- Soldering is a method used to solder mostly commonly aluminum components in electric industries mainly chipsets, wires, processors, circuits, etc.
- In soldering the melting temperature of filler material is less than 430 degree Celsius which is also less than the temperature of base metal
- The filler material used in soldering is made up of an alloy of lead and tin.
- The heat source used in soldering is generally in the form of soldering irons or torches
Brazing
- Brazing is a method in which the melting temperature of filler material is more than 430 degrees Celsius, but less than the melting temperature of the base material.
- To weld aluminum using a brazing technique requires a filler material that is placed between the lying surface to be joined.
- The filler material used is an alloy of copper and zinc, copper, and silver.
- The strength of a brazing is more as compared to soldering.
- Commonly used for pipe fittings where leak proof joints are required.
Joint types for Aluminum welding using TIG and MIG welding
- T joint
- Corner joint
- Single bevel joint
- Square butt joint
- Square joint with backing
- Flange joint
- Edge joint
- Single V- joint
Filler material and Shielding gas used in welding Aluminum
Filler material
There are various filler materials used in aluminum welding, the filler material ranges from pure aluminum to a combination of aluminum with different materials (filler alloys) such as silicon, magnesium, zinc, etc.
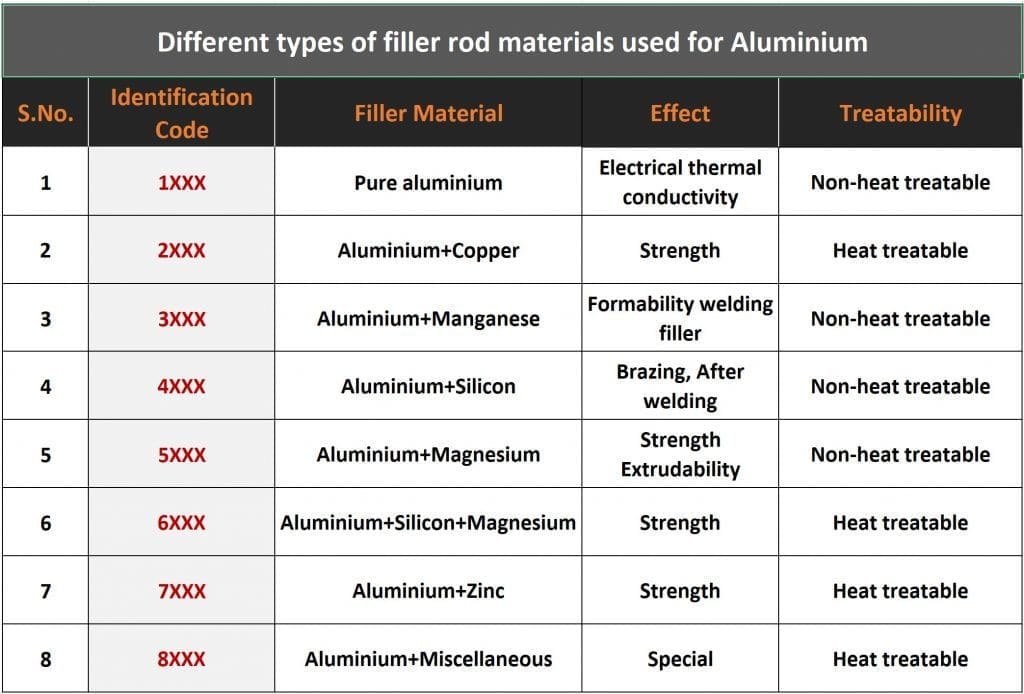
- 1XXX, 2XXX. 3X.., implies that there are various sets of filler materials available for welding, which are identified on the basis of their alloying elements such as magnesium, silicon, silicon+magnesium, etc. coded with numbers for their identification.
- The filler alloys are categorized on basis of heat-treatable and non-heat-treatable alloys.
- This coding will help us to decide the filler material, which will go best with our welding on the basis of our requirements( effect and treatability).
Shielding gas
- The function of shielding gas is to prevent the weld pool from the attack of atmospheric gases which can cause defects such as access Oxide formation, weld inclusions, weld porosity, etc.
- Shedding gas used in aluminum welding are helium, neon, argon nitrogen, and carbon dioxide most commonly used shielding gas is pure argan, pure helium, or a mixture of argon and helium
- Flow rates of 20 to 30 cubic feet per hour are recommended.
Problem related to Aluminum welding
- Aluminum reacts strongly with oxygen in the presence of direct current straight polarity forming oxide Al2O3.
- The oxide layer formed is very strong and tough due to which it can easily cause weld defects, due to a higher density of oxide it may sink into the weld pool where it can result in welding inclusions.
- The oxide layer formed on the surface of aluminum results in a considerable impact on the welding. If the oxide layer is not removed before welding it can cause many weld defects and can impact the strength of the weld.
The oxide layer is generally cleaned using a steel-wired brush after each run.
Defects in Aluminum welding
1- The corrosion resistance of welded material
- While welding aluminum thermal cracks are generated, if those thermal cracks are left and unrepaired then corrosive media can easily find their way into them so that erosion can continue in the interior cracks found in the weld.
- To increase the corrosion resistance the welded area is heat-treated after the welding process.
Note:
Be very careful while using filler material for aluminum, remember to check its treatability whether it is heat treatable or not.
2- Discontinuities in weld
- Discontinuities in aluminum words are usually caused due to inadequate joint preparation and cleaning.
- Cracks and poor fusion are serious discontinuities but the most common are pores formation.
- Discontinuity in the weld is a form of welding defect that it occurs due to the following reasons:-
- Cracks
- Poor or Incomplete fusion
- Oxide inclusions
- Incomplete penetrations
- Cavities
- Undercuts
- Pores
3- Oxide formation
- An excessive layer of oxide formation on the surface of the weld, if the base plate temperature reaches too high.
Ways to Avoid defects
There are a number of ways of reducing defects generated during welding of aluminum, some of these include:-
- Removing the oxide layer.
- Inspection of feed rollers in MIG welding.
- Adjusting the angles of welding gun/torch.
- Ensure a good and proper supply of shielding gas.
- The contact tip of the electron and the gas spreaders must be properly cleaned and defect-free.
Note:
Aluminum is a highly reactive metal which means that it can quickly and easily react with oxygen present in the atmosphere to form a thin layer of oxide which provides good corrosion protection but at the same time, we need to understand that if that oxide layer is not broken down during the welding process, may result in welding defects.
So, while applying the second layer of welding make sure that the joint and nearby areas of the weld must be carefully cleaned by means such as filing, scraping, brushing, or washing.